Software & Technology
Autodesk CAM Solutions
Improve and automate computer-aided manufacturing workflows for CNC machining.
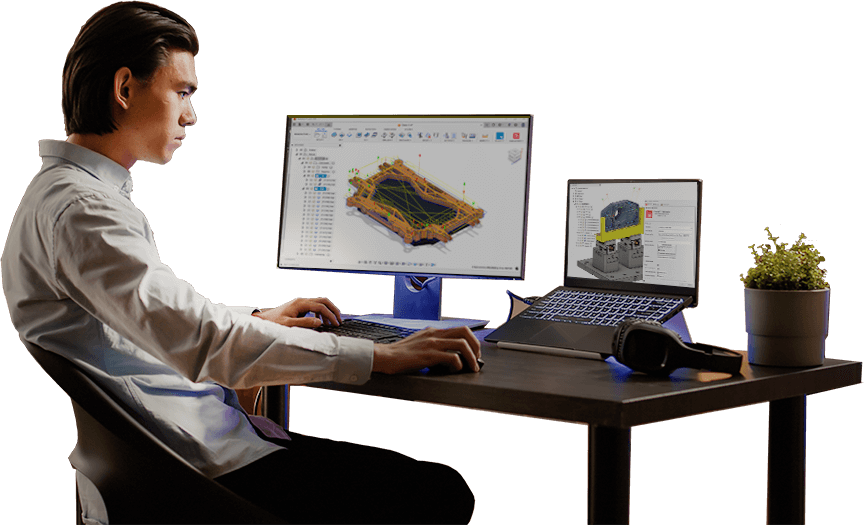
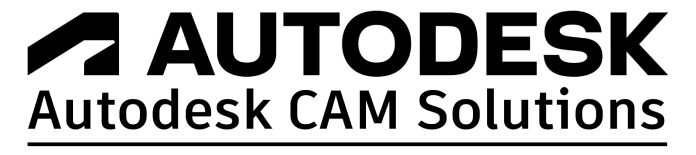
Overview
Welcome to the future of advanced manufacturing! Autodesk CAM (Computer-Aided Manufacturing) products are changing the way we manufacture and provide powerful tools that integrate seamlessly with your workflow. Autodesk’s suite of CAM solutions is designed to elevate your productivity, precision, and performance, ensuring you stay ahead in a competitive industry. Explore how Autodesk CAM products can transform your design and manufacturing processes, from concept to completion.
Benefits of Autodesk CAM Solutions?
- Integrated Workflows: Experience the seamless integration of CAD and CAM in a unified environment, reducing errors and enhancing efficiency.
- Advanced Toolpaths: Leverage sophisticated toolpath strategies to maximize machine performance and achieve superior surface finishes.
- Flexibility and Scalability: Whether you are a small workshop or a large manufacturing plant, our CAM solutions scale to meet your needs.
- Cutting-Edge Technology: Stay ahead with the latest advancements in CAM technology, powered by Autodesk’s continuous innovation and development.
- Expert Support and Community: Access a vast network of resources, including expert support, training materials, and a vibrant user community.
Digital Tools by Autodesk for Advanced Manufacturing Experts
Autodesk Fusion
A comprehensive solution combining CAD, CAM, and CAE in a single platform. Perfect for rapid prototyping and complex machining tasks. Fusion integrates design, engineering, and manufacturing into one platform, allowing for efficient and streamlined workflows.
Autodesk FeatureCAM
Automate your CNC programming with FeatureCAM’s intuitive features, reducing programming time and increasing efficiency. FeatureCAM simplifies the process of going from design to finished part, enabling faster, more consistent, and more reliable results.
Autodesk PowerMill
Specialized for high-speed and complex machining, PowerMill offers unparalleled control over your manufacturing process. PowerMill is ideal for creating intricate molds, dies, and other complex shapes, delivering exceptional precision and quality.
HSMworks
Integrated CAM for Inventor and SolidWorks users, providing efficient toolpath generation and powerful machining capabilities. HSM delivers best-in-class integration with your existing CAD environment, offering high-performance machining tools that improve productivity and quality
Autodesk Fusion Operations
Fusion Operations is production management and floor tracking software that allows you to schedule and manage teams, machines, and materials efficiently. It provides real-time production visibility powered by shop floor devices, enabling you to track and analyze your entire production flow. With integrated maintenance management, you can easily track operations and plan future actions.
Solutions Supporting Autodesk Technology
SolidCAD is dedicated to expanding its technology partnerships to enhance and streamline the machining processes and workflows of our clients. Our approach focuses on curating a technology stack that integrates seamlessly, allowing for a more holistic view and capability of updating the entire workflow.
Seamless Integration
We prioritize technologies that can be easily integrated into existing systems to minimize disruption and maximize efficiency.
Continuous Innovation
We are committed to a continuous search for cutting-edge technologies that can further refine and improve our clients’ machining workflows.
Exploration of Add-ons
We actively seek and incorporate add-ons from various vendors to enhance functionality and adaptability.
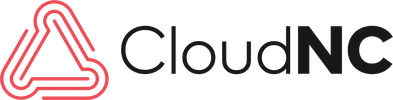
Precision Machining with AI-Driven Automation for Fusion
Cloud NC complements Autodesk CAM solutions by providing advanced, automated CNC machining capabilities. Utilizing AI and machine learning, Cloud NC optimizes toolpaths and machining strategies for superior precision and efficiency. Integrate Cloud NC with Autodesk tools for enhanced productivity and quality.
Key Features
AI-Driven Automation: Automate complex CNC programming tasks for increased consistency.
Optimized Toolpaths: Achieve faster machining times and higher-quality finishes.
Seamless Integration: Smooth integration with Autodesk solutions for cohesive workflows.
Scalable Solutions: Suitable for small workshops to large facilities.
Enhance your Autodesk CAM solutions with Cloud NC for advanced automation and optimization in CNC machining.
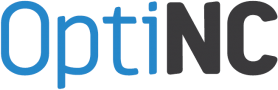
Explore OptiNC: Integration with Autodesk PowerMill for Automated Machining
Opti NC’s product focuses on enhancing manufacturing efficiency through advanced process optimization. This software solution utilizes sophisticated algorithms and machine learning techniques to streamline and improve manufacturing workflows, particularly beneficial for industries relying on precise and efficient machining operations.
Key Features
Advanced Algorithm Integration: Employs cutting-edge algorithms to optimize tool paths, reducing machine time and increasing productivity.
Machine Learning Capabilities: Leverages machine learning to continuously improve process efficiency by analyzing and learning from data patterns.
Seamless Integration with PowerMill: Designed to integrate effortlessly with Autodesk’s PowerMill, ensuring a smooth workflow and enhanced usability.
Real-Time Analytics and Reporting: Provides real-time insights into manufacturing processes, allowing for immediate adjustments and improved decision-making.
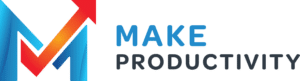
MAKE Productivity: A Solution made for education and learning for PowerMill Automation
MAKE Productivity serves as an invaluable learning tool for students and educators in automated machining processes. It enhances educational programs focused on CNC machining and advanced manufacturing with practical, hands-on technology experiences.
Key Features
Interactive Learning Modules: Allows students to apply advanced algorithms in practical machining scenarios.
Guided Simulations: Provides safe, realistic simulations of manufacturing processes for in-depth learning.
Seamless Educational Integration: Works effortlessly with platforms like Autodesk’s PowerMill, facilitating easy incorporation into curricula.
Progress Tracking and Analytics: Offers tools for monitoring learning progress and identifying improvement areas, supporting both students and educators.
SolidCAD for Comprehensive CNC Machining Consulting and Implementation
SolidCAD offers services to streamline your CNC machining processes, ensuring maximum efficiency and productivity.
- CNC Programming and Customization: Create and customize CNC programs and post processors.
- Machine Tool Integration: Select and integrate the right machine tools for your needs.
- Process Optimization: Implement automation to increase accuracy and efficiency.
- Training and Support: Provide training and ongoing support for your team.
- Additional Tools and Technologies: Integrate complementary tools to enhance capabilities.
SolidCAD provides the expertise, tools, and support needed to optimize your CNC machining processes for the highest levels of efficiency and productivity.
Why Choose SolidCAD?
Specialized Expertise in Advanced Manufacturing
We pride ourselves on our designated team of experts specializing in advanced manufacturing, CAM, and CNC machines. Our team’s extensive knowledge and experience ensure that you receive the highest level of service and support for all your manufacturing needs.
Advanced Programming and Consulting Services
We offer specialized consulting and implementation services tailored to your specific requirements. Our advanced programming capabilities allow us to optimize your CAM processes, enhancing productivity and efficiency across your operations.
Access to Cutting-Edge Tools and Technology
SolidCAD provides additional tools and access to the latest technology to enhance your software capabilities. Stay ahead of the competition with our innovative solutions that integrate seamlessly with your existing systems, driving superior performance and results.
Dedicated Support and Mentoring
Our commitment to your success goes beyond implementation. We offer dedicated support and mentoring, ensuring you maximize the benefits of your CAM software. Our team is always available to provide guidance, troubleshoot issues, and help you achieve your goals.?
Industry Experience and Knowledge
With years of experience and in-depth industry knowledge, SolidCAD understands the unique challenges and opportunities within the manufacturing sector. Our expertise enables us to deliver customized solutions that address your specific needs, ensuring you stay competitive in a rapidly evolving market.
Success Stories
Get Started with SolidCAD Today
Ready to revolutionize your manufacturing process? Contact our sales team for a personalized consultation or start your free trial to experience the power of Autodesk CAM products firsthand.
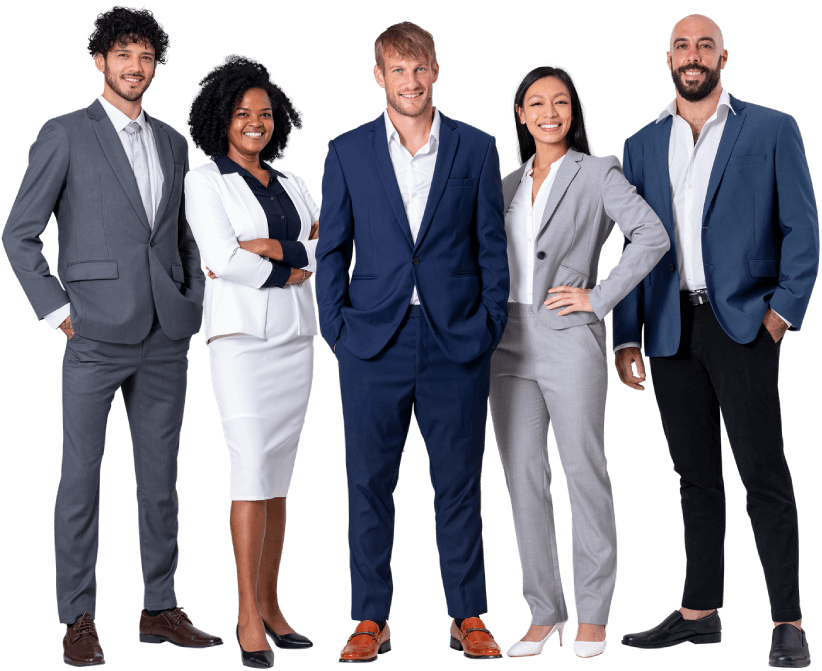