Success Stories
Société de Transport de Montréal (STM)
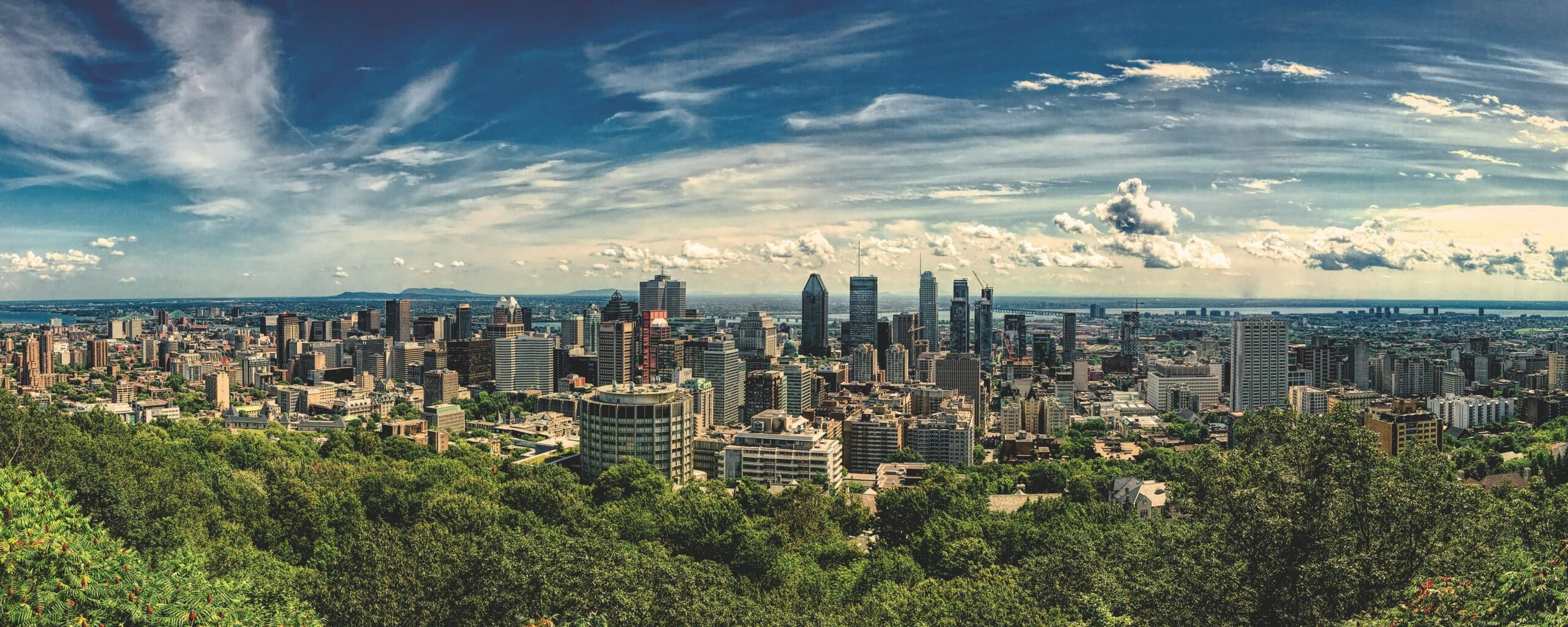
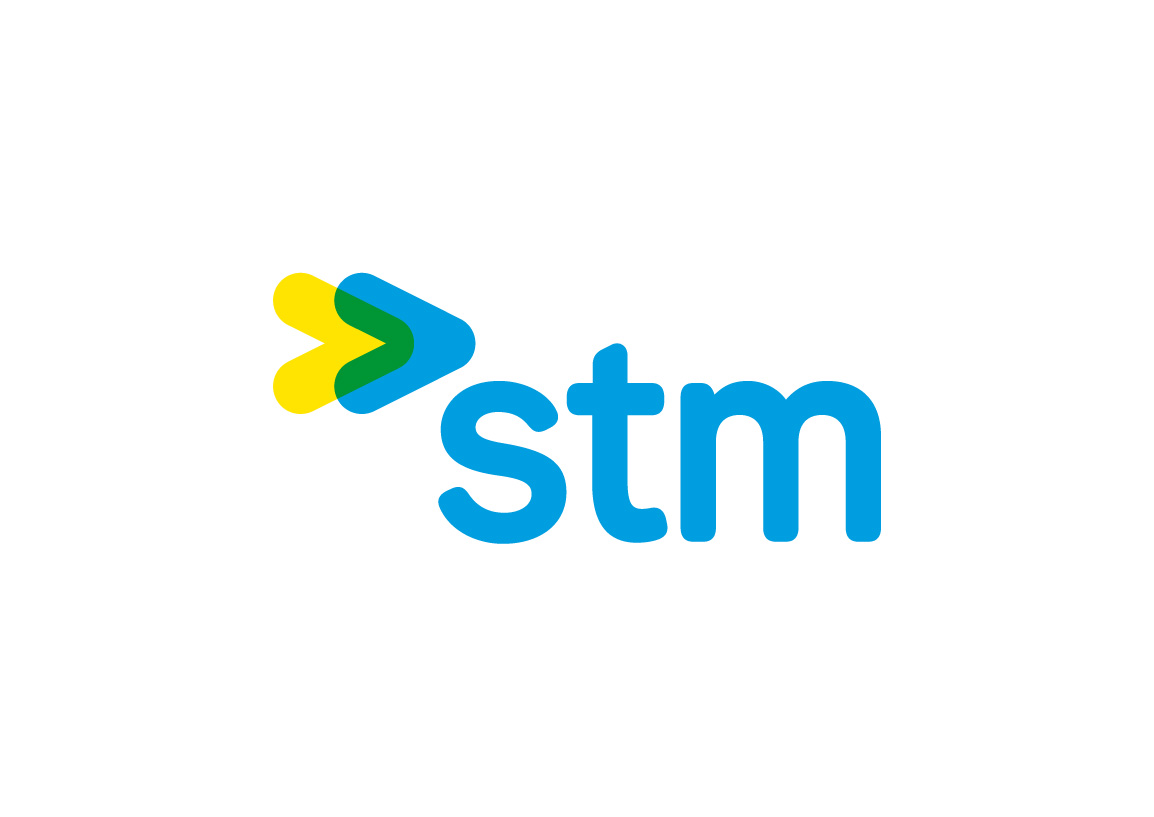
Summary
Public transportation – buses, trains, subways, and more – have a wide range of complex assets that are both mobile and stationary. Upgrades, expansions, and new assets become intricate engineering projects involving a broad array of information and documents.
Hardcopy and manual methods for managing this information and changes are ad hoc and unreliable – causing engineers to use outdated information. This spawns rework, cost increases, schedule delays, and conditions out of specification. This chaos is brought under control with Accruent Meridian’s software for managing engineering information. As a result, projects are more likely to meet the leading KPIs for on-time, in-budget, and within spec.
Engineering information management reduces rework and helps assures completion of projects on-time, in-budget, and on-schedule.
Société de Transport de Montréal uses Accruent Meridian in its engineering teams for information management and business process automation replacing unreliable ad hoc manual methods. |
Société de Transport Montréal (STM)
Public transportation has existed in Montréal for over 150 years, starting with horse-drawn tramways in 1861. Société de Transport de Montréal (STM) became a public corporation in 1951 with the mission to provide Montrealers with fast, reliable, economical transit service. The company now has over 11,000 employees.
Large Infrastructure with Complex Assets
From its beginnings in 1861, STM has grown to include four subway lines with 68 stations and over 1,000 cars. The bus system includes 186 bus routes and over 2,000 vehicles. Its paratransit service has 80 mini-buses and other taxi services for people with mobility issues. The infrastructure is widely distributed throughout the city, including rail lines, switchgear, signaling, rail yards, bridges, ticketing stations, bus stops, depots, garages, offices, and more. STM has a wide variety of complex assets.
The consultation
First used in Paris, France in 1951 and then Montreal, Canada in 1966, the passenger trains use wheels containing both rubber tires for improved traction and traditional railway steel wheels for guidance through conventional switches. Montreal has steep hills with inclines beyond the capability of steel wheels alone. Engineering projects and maintenance occur throughout the bus and rail infrastructure. The maintenance shop performs upgrades and repairs for the trains.
Substantial Investment Plan
STM’s “Organizational Strategic Plan 2025” provides a 10-year strategy, including many bus and metro projects. The C$8 billion investment plan for 2015 to 2025 focuses on improving customer transit experience. The plan initiates a shift that aims to both qualitatively and quantitatively improve the customer experience. Environmental, social, and governance (ESG) initiatives like converting to electric buses are also included.
Project Execution Barriers
The strategic plan involves many projects to engineer the design, procure materials, construct upgrades and obtain new assets. Fundamental to the success of the plan requires an examination of STM’s engineering software tools.
Engineering Project Execution
The execution of the plan involves a complex set of timed engineering projects with performance penalties if behind schedule. A study by McKinsey has shown that 98 percent of projects are completed behind schedule and over budget. Obviously, this poor performance would have a serious negative impact on STM’s strategic plan.
Large Ecosystem for Engineering Projects
STM engages with multiple contractors across various projects involving trains, buses, stations, and related infrastructure. This ecosystem includes about 20 major contractors, hundreds of smaller contractors, and their subcontractors. Individual engineers and contractors phase in and out of a project over its lifespan of 5 to 8 years.
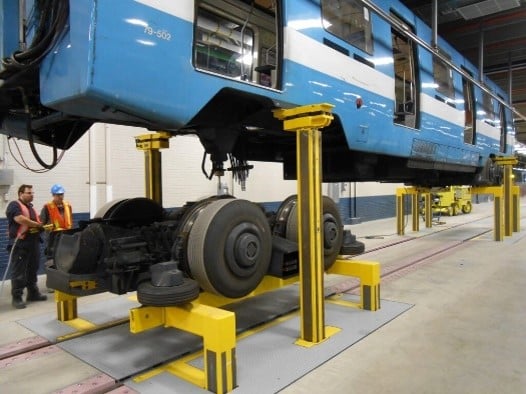
Evils of Balkanized Engineering Data
Storing and managing engineering information using hardcopy documents in file cabinets is problematic. Engineers typically spend 30 percent of their time searching for information, which negatively impacts productivity. Too often, they also end up with older versions. Perhaps a holdover from hardcopy prints in file cabinets, each siloed engineering department stores its copy of drawings with its markups. Unfortunately, older versions of the documents are retained, and the markups are not shared.
When an engineering department edits a document or makes a change that affects another department’s records, the change stays local and is not known by others. Hardcopy documents and Adobe files in a server do not accommodate automated business processes for synchronization across silos. Manual processes – like remembering to send an email – often fail. This issue gets magnified with the ecosystem of contractors and subcontractors involved in a project. Balkanized engineering data leads to using outdated information, rework, schedule delays, and cost overruns.
Weak Information Management Compromises Project KPIs
The key cause of poor project performance involves the use of outdated engineering information and documents. This cascades into many problems, including ordering of wrong materials, fabricating components out of specifications, construction errors, and a variety of other issues. Recovery requires rework that adds costs and creates schedule delays. Sometimes the rework cannot fully bring the work back within specifications causing design compromises. The project KPIs – on-time, in-budget, and within specifications – are compromised.
Modernization Enabler
Fundamental to the execution of a project within the common leading KPIs – on-time, inbudget, and within specs – is getting all participants “on the same page” and using current information. This includes the extended enterprise comprising STM’s engineers, suppliers, and subcontractors.
Common Engineering Information
Asset information changes many times during an asset’s lifecycle, from asset creation through operations and maintenance and to end-of-life. Data about the asset are handed over numerous times from engineering, procurement, and construction (EPC) firms; supply chain partners; owner-operators; and internally within each of these organizations. Valuable data can be lost, misinterpreted, or keyed in incorrectly. Tag and equipment data are difficult to manage because they are often in differing formats, exist in various applications and systems, and transmitted by different means. Naming conventions and asset hierarchy provide additional avenues for divergence.
Managing asset information is difficult among balkanized organizations with independent workflows and KPIs. Balkanized data is often found in mutually distrusting and sometimes hostile groups or functions within an organization. This dysfunction commonly involves the design/build process for assets among the engineering, procurement, and construction functions. It also occurs during the operate and maintain phase of an asset’s lifecycle for reliability engineering, maintenance, control engineering, and others. A common repository for asset information breaks through these barriers by connecting silos to provide access to data and information. This enables an integrated view of the asset’s information, documentation, and data throughout its lifecycle across the traditionally siloed functional perspectives.
Fit Types of Users
STM organized access to the engineering data via mobility devices along three types of users:
- Engineering software application user
- Technician executing a work order
- Casual user including subcontractors and management
Each type of user has specific permissions that fit their roles. This includes organization, locations within that organization, physical location, and permission levels. Permissions has two choices i.e., read/write access, or read only which does not permit editing.
Business Process Automation
Business process execution involves cross-functional activities. For example, a change in the maintenance strategy for an asset by the reliability team evolves into changes needed in other areas like maintenance or inspections. Manual approaches, such as email, phone calls, or paperwork orders, are unreliable, often leading to lost alerts and continuing with the old way of doing things. Business process automation ensures that the alerts go to the correct people and the needed action can be confirmed. In addition, a dashboard provides visibility to open alerts.
Meridian Implementation
SolidCAD has been partnering with STM for the last 20+ years to implement, support and train resources with Meridian.
Being the largest Autodesk partner and the only Accruent Meridian partner in Canada brought extensive value to STM, as SolidCAD has been able to deliver tailor made configurations to different engineering departments within STM. Software such as AutoCAD, Civil 3D, Inventor or even Revit are heavily used and generated file formats are handled in Meridian.
When an engineer opens a document in any of these CAD platforms, the file comes from the Meridian server for the engineering information. Saved changes also go into Meridian.
Conclusion
STM has been using Accruent Meridian since 2001. With each new project, its use expanded and now encompasses 12 different engineering departments for a wide variety of assets – buses, trains, lines, and infrastructure. It has proven to substantially reduce the use of the wrong document version and the associated rework. This also improved engineering productivity by nearly eliminating searching for information. The reduced rework and improved engineering productivity enables delivery of projects on time, within budget, and within specifications.
For further information or to provide feedback on this article, please contact your account manager or the author at rrio@arcweb.com. ARC Views are published and copyrighted by ARC Advisory Group. The information is proprietary to ARC and no part of it may be reproduced without prior permission from ARC.