In short, yes. By design, Meridian is an engineering document management system (EDMS). But once in use by Engineering, the tool can be extended to support more general content management needs and maximize your software investment.
How? By definition, enterprise content management is a system designed to collect, organize and manage an enterprise organization’s content. This includes unstructured documents – like those found in a Word file, an excel spreadsheet, or a PDF and everything in between. An enterprise content management system is rarely, if ever, one tool but rather a combination of tools, processes, and strategies used to organize information and improve business performance.
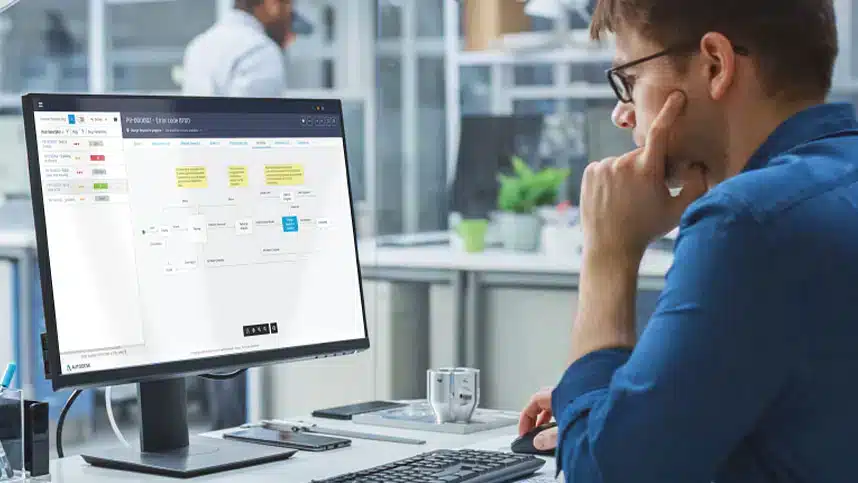
The goal is to:
- Eliminate dependence on paper documents
- Maximize employee efficiency
- Improve productivity and customer service
- Streamline and automate business processes
- Make business-critical information both accessible and valuable
- Improve collaboration
Because it can easily handle both structured and unstructured documentation – like CAD drawings, engineering documents, and technical manuals – Meridian can streamline content management needs.
Plus, with our powerful workflows and version control, we can ensure everyone in the organization is working from a true single source of truth.
What Can Meridian Provide For General Enterprise Content Management System Do?
An enterprise content management system helps with document management throughout the lifecycle. In other words, it allows users to:
Capture information
Users can easily and securely enter data into an ECM. This can include invoices, emails, PDF documents, spreadsheets, etc. Effective content capture can take many forms, like using electronic forms, scanning documents, or managing documents that are already digital.
Manage and retrieve documents
Will well-managed and organized documents, all relevant users can easily access business-critical information. This can be done in many ways, including full-text search, keyword search, or preset search options that allow users to search by creation date, username, or other factors.
Store
With a robust ECM, users can easily store all their documentation. The key? To make the information accessible and searchable. That way, users can easily view documents, edit them, organize them, view the metadata, and more. This, in turn, can improve compliance and reduce the time and complexity associated with document management processes.
Preserve or Archive: Users can also preserve – or archive – information that doesn’t need to be readily available but may prove vital in the future.
Deliver
Finally, users can use the ECM to deliver the right content to the right people at the right time. Today, this will include a significant degree of automation, which can streamline manual tasks and help teams accomplish more with fewer resources.
Why Do Organizations Need Content Management?
Organizations need enterprise content management to help them organize, manage and utilize all the content they have coming in today. And this is more important than ever, as organizations have information coming from more sources than ever before. Emails, spreadsheets, documents, presentations – the volume of data is staggering, and it is only growing as organizations continue to mobilize, digitize and adopt new systems and tools.
In this context, effective content management is critical, as it’s the only way that team members can maximize efficiency, make decisions, manage risks. Improve record management and complete projects.
Is Enterprise Content Management the Same As Document Management?
It can be. Document management will always be a smaller but essential part of content management (which, as we mentioned, necessarily also includes best practices, strategy, and supporting tools). That said, with the bevy of content we have coming in today – from thumb drives, smartphones, apps, email, social media, video, paper sources, and more – not all content management will come from documents.
However, the content that does come from documentation will have to be well managed. That’s where a tool like Meridian can help significantly.
General document management systems like SharePoint, for example, can organize linear, largely static documentation. A blog document, for example, can be stored and accessed in SharePoint because that document is usually created, edited, posted, and archived. And a general system can handle that process.
However, a typical ECM cannot handle complex documentation like engineering information. This kind of documentation – which many organizations have today – must be regularly redlined, updated, and utilized to reflect the business’ actual environment. Meridian is unique and can provide a complete EDMS & ECM solution. Meridian is tailor-made to handle this kind of documentation and workflow, so this complicated documentation never falls through the cracks.
Does Enterprise Content Management Help With Both Structured And Unstructured Data?
Not well. There have been many new content management challenges and opportunities with machine learning, cloud technology, and mobile capabilities. Today’s content management systems must handle:
- Unstructured information, or information without a fully defined structure that people frequently use. Examples include PDFs and Word documents
- Structured information, or information that is highly defined and quickly processed by computers. This includes information that is housed in databases
- Semi-structured information, or information (like invoices or receipts) that is defined by a human then stored and read by a computer
This, in turn, can help organizations battle issues that accompany poor data management, including lost time, lost productivity, compliance concerns, and more. Most general ECM tools cannot get this done.
What Are the Benefits of Effective Content Management?
There are many benefits to excellent content management, including:
- Improved efficiency and business continuity
- Streamlined compliance and improved record retention policies
- Fewer paper documents, which can lead to increased efficiency and enhanced collaboration
- Less downtime and document search time
- Reduced time and overhead costs associated with document storage and document management
- Automated manual tasks
- Improved document security (which is achieved through restricted access and controlled access)
- Reduced duplicate or outdated information
- Improved customer satisfaction achieved through increased employee productivity
How Can I Start Implementing the Right Content Management System For My Business?
If you’re considering implementing an enterprise content management system, you should first consider:
- Your organization’s short and long-term business goals and how you would like your content management tool to help you achieve those goals
- The various types of content that are included in your business and how your organization handles those types of content. Do you have unstructured engineering documentation? Is that documentation static?
- Your existing processes and how you would like your EDMS to streamline those functions
- How information is shared and utilized by your employees and departments
- Your business culture and whether your team is ready to adopt a new system and enact change
Getting this information straight can help you determine exactly what features and functionalities you need from your system. From there, you can get into the nitty-gritty of the implementation. Here, it’s important to remember to:
Prioritize the most mission-critical documentation and areas that need improvement.
Get your team on board and bought into the tool you choose by explaining the vision and showing them concrete benefits and expected results.
Invite feedback, so you fully understand what your team expects and needs.
Create a dedicated team to oversee the implementation process.
Ensure that there are clear ECM policies and rules in place. This will prevent the mismanagement of data.
Embrace the growing pains. No technology implementation is ever super smooth. Expect the unexpected and be ready to adjust course when it’s necessary.
To learn more about Meridian solutions (EDMS and CMMS) and how they can help your team, don’t hesitate to get in touch with the SolidCAD Meridian team.