The construction industry is undeniably a crucial pillar of Canada’s economy and society. However, in the 21st century, it faces a multitude of challenges and opportunities, including workforce shortages, climate change concerns, evolving customer expectations, and fierce global competition. In this context, digital technology emerges as a key driver and enabler of innovation and transformation within the construction sector.
While digital transformation is sweeping through the industry, not all construction companies have embraced it with equal fervor. Some have emerged as early adopters, blazing the trail, while others have been more cautious, following suit at their own pace. Additionally, the adoption of digital technology varies across different regions and segments of the construction industry. In this blog post, we will explore how the Canadian construction industry compares to its global counterparts in terms of digital technology adoption and delve into the underlying reasons. We will also discuss how proper custom training and implementation can address the technology adoption challenge, as well as why construction companies should move away from Excel and emails. Finally, we will discuss the way forward for the Canadian construction industry in the digital era.
How does the Canadian construction industry compare to the rest of the world in terms of adopting digital technology and why?
According to a report by McKinsey & Company, the global construction industry has been one of the least digitized sectors, ranking only above agriculture and hunting. The report estimated that if the global construction industry fully embraced digital technology, it could increase its value added by $1.6 trillion per year, or 2 percent of global GDP.
But the report also noted that there are significant variations in the level of digitization across regions and segments of the construction industry. For instance, Europe and North America have been more advanced than Asia and Africa in terms of adopting digital technology in design and engineering. However, Asia has been leading in terms of adopting digital technology in construction and operations. Moreover, some segments of the construction industry, such as infrastructure and industrial projects, have been more digitized than others, such as residential and commercial projects.
According to a survey conducted by KPMG in Canada and the Canadian Construction Association (CCA) in 2020, the Canadian construction industry has been lagging behind other industries in Canada, as well as other regions in the world, in terms of adopting digital technology. The survey found that only 25 percent of Canadian construction companies felt like they were in a considerable or great position relative to their competitors in terms of technology or digital implementation, compared to 47 percent globally. The survey also found that only 23 percent of Canadian construction companies said their decisions were supported by and based on data to a considerable or great degree, compared to 36 percent globally.
The survey identified several challenges and barriers that prevent Canadian construction companies from adopting digital technology more quickly, such as lack of skills or talent, lack of budget or funding, lack of leadership or vision, resistance to change, lack of awareness or understanding, and lack of collaboration or integration. The survey also highlighted some drivers and benefits of digital transformation in the Canadian construction industry, such as improving productivity, increasing efficiency, enhancing customer satisfaction, reducing costs, increasing profitability, and improving quality.
One of the indicators of digital adoption in the construction industry is the use of software tools for project management and collaboration. Here’s a little treat for you for reading this post so far. In a lighthearted twist, I turned to an AI model to generate a prediction based on the adoption of Excel compared to popular alternatives like Procore and Autodesk. Although the AI’s prediction may not fully satisfy the parameters and assumptions required for an accurate projection, let’s take it in good spirits and have some fun exploring its findings.
The attached graph shows the adoption scale of Excel, Procore, and Autodesk Construction Cloud among Canadian construction companies from 1985 to 2025 (projected):
*Projected values based on current trends and assumptions.
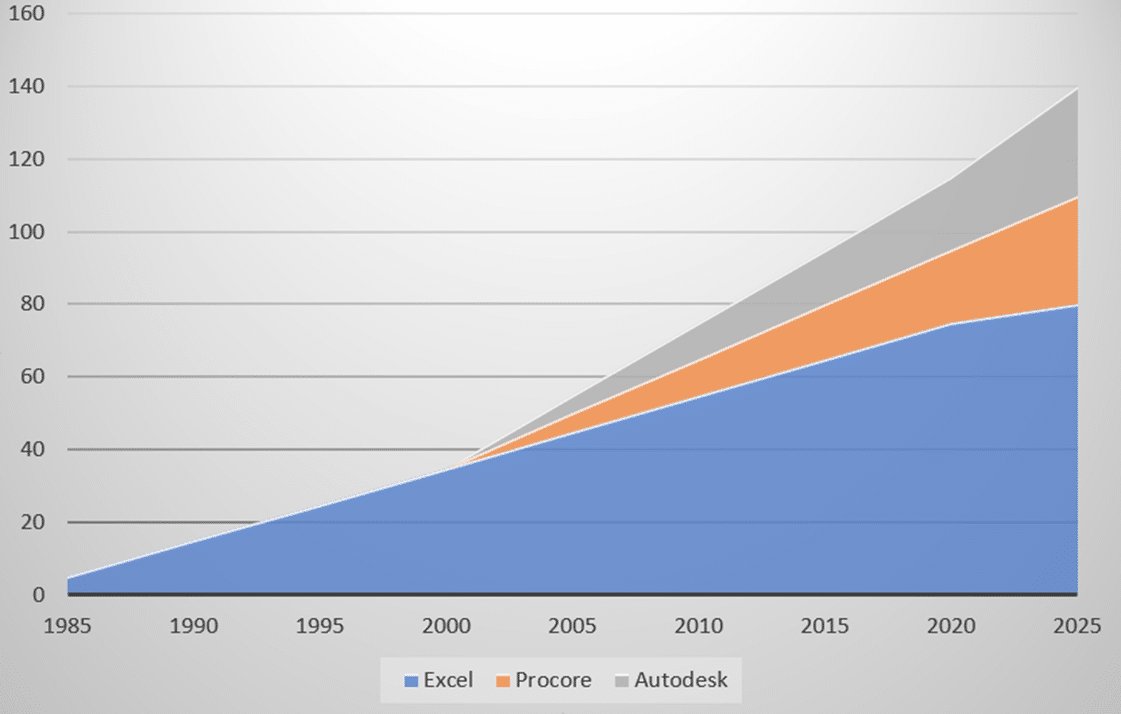
The graph shows that Excel has been the dominant tool for construction companies since its introduction in the mid-1980s, and has steadily increased its adoption rate over the years. But it also shows that Procore and Autodesk Construction Cloud have emerged as viable alternatives in the past decade, and have gained some market share from Excel. It’s worth noting that Autodesk Construction Cloud as we know it, has evolved over the years and many may know this platform by Plangrid, Bim 360 Build or Build. The graph also projects that by 2025, Procore and Autodesk construction cloud will have increased their adoption rates by another 10%, while Excel will have reached a plateau at around 80%. This suggests that construction companies are becoming more aware of the benefits and limitations of Excel, and are exploring other digital solutions that can offer more integration, collaboration, and innovation.
“I skate to where the puck is going to be, not where it has been. – Wayne Gretzky”
Disclaimer: My AI friend claims that the data for this graph was obtained from various sources, such as industry reports, surveys, interviews, and websites, and that the assumptions for the projections were based on the current trends and growth rates of the software tools, as well as the expected changes in the market and customer preferences, but I digress.
How can proper custom training and implementation address the technology adoption challenges?
One of the main challenges that Canadian construction companies face when adopting digital technology is the lack of skills or talent to use or implement the technology effectively. Going back to the survey by KPMG and CCA, 49 percent of respondents said that finding or developing people with the right skills or expertise was a major challenge for their company.
To overcome this challenge, construction companies need to invest in proper custom training and implementation programs that can help their employees learn and adopt the technology in a smooth and efficient manner. Some of the best practices for successful construction technology implementation include:
- Getting buy-in from the entire team, from executives to end-users, by showcasing how the technology will drive value for them and addressing their concerns or feedback.
- Setting a clear timeline and milestones for the implementation process, and assigning roles and responsibilities to each team member involved.
- Understanding the existing workflows and company structures that will be impacted by the technology, and customizing the solution to fit the specific needs and goals of each project or division.
- Involving employees in the training process, and providing them with continuous support, feedback, and resources to help them apply their knowledge in the field.
- Measuring and communicating the success and outcomes of the implementation process, and celebrating the achievements and improvements along the way.
By following these best practices, companies can ensure that their employees are well-equipped and motivated to use and implement digital technology effectively and that they can maximize the return on investment of their technology solutions.
Why should construction companies move away from Excel and Emails?
Another challenge that Canadian construction companies face when adopting digital technology is the resistance to change from internal stakeholders who are used to working with traditional tools such as Excel and emails. Why fix something that’s not broken? Looking back at the survey by KPMG and CCA, 50 percent of respondents said that overcoming resistance to change was a major barrier for their company.
Internal development is never easy. The growth of a company can be compared to the growth of people on a personal level as well. This reminds me of the famous analogy of lobsters by Dr. Jordan B. Peterson. Stay with me here! So, lobsters, they grow by molting. Picture this: they struggle and break free from their old shells, all the while absorbing water that expands their body size. Talk about a transformation! Now, this molting process happens around 25 times in the first 5-7 years of a lobster’s life. And it’s no walk in the park. But guess what? It’s absolutely necessary for their growth.
You see, as company owners, the weight of leadership falls on your shoulders. It’s up to you or your leadership team to ensure that your team members understand the rewards that come with staying up-to-date in our ever-evolving industry. When the benefits become crystal clear, the cost of keeping pace is no longer a concern.
There are actually many reasons why construction companies should move away from Excel and emails, and adopt more advanced and specialized software tools for project management and collaboration- even if that means going through temporary pain. Some of these reasons include:
- Excel and emails are prone to errors, inconsistencies and duplication, which can lead to inaccurate data, miscommunication and rework.
- Excel and emails are not designed for collaboration, which can result in silos, delays, and conflicts among project stakeholders.
- Excel and emails are not scalable or adaptable, which can limit the growth, innovation, and efficiency of construction companies.
- Excel and emails are not secure or compliant, which can expose construction companies to data breaches, cyberattacks, and legal risks.
By moving away from Excel and emails, construction companies can benefit from software tools that are specifically designed for construction project management and collaboration. These tools can offer features such as:
- Real-time data capture, analysis, and visualization, which can improve decision-making, transparency, and accountability.
- Cloud-based storage, access, and sharing, which can enhance mobility, flexibility, and connectivity.
- Workflow automation, integration, and standardization, which can increase productivity, quality, and consistency.
- Data protection, encryption, and backup, which can ensure security, compliance, and reliability.
By adopting these software tools, construction companies can improve their performance, efficiency, quality, and safety on their projects, as well as create a competitive edge in the market.
What is the way forward for the Canadian construction industry in the digital era?
The Canadian construction industry is keen on promoting innovation and driving digital transformation. Advances in technology, like artificial intelligence, drones, and 3D modeling, along with improved project delivery models, are reducing waste, boosting productivity, and enhancing sustainability. The industry calls for increased investment in research and development, education and training, and collaboration to accelerate this transformation.
To thrive in the digital era, the Canadian construction industry should focus on these key areas:
- Building a digital culture: Foster an innovative and digitally-ready mindset across the organization, from top management to frontline workers.
- Developing digital skills: Invest in training and upskilling programs to equip the workforce with the necessary expertise in digital tools, data analysis, digital workflows, and cybersecurity.
- Embracing collaborative platforms: Adopt collaborative platforms and project management tools to streamline communication and enhance project coordination.
- Implementing advanced technologies: Embrace technologies like Building Information Modeling (BIM), drones, robotics, and IoT for better project visualization, data-driven decision-making, automation, and safety.
- Leveraging data analytics: Utilize data analytics to gain insights, optimize operations, and make informed decisions by analyzing data from sensors and construction management software.
- Prioritizing cybersecurity: Protect sensitive project data, intellectual property, and client information through robust cybersecurity measures and employee education.
- Collaborating with technology providers: Partner with technology providers, startups, and research institutions to access innovative solutions and industry insights.
- Promoting industry-wide standards and best practices: Standardize processes and adopt best practices to facilitate interoperability, data exchange, and collaboration among stakeholders.
By embracing digital technology and implementing these strategies, the Canadian construction industry can overcome barriers, drive digital transformation, and achieve improved productivity, efficiency, and sustainability. This will contribute to the industry’s growth and success in the digital era. And here at SolidCAD, we can help.
Learn More:
- constructionblog.autodesk.com
- constructionblog.autodesk.com
- buildertrend.com
- procore.com
- Imagining construction’s digital future