Success Stories
Whelan Construction
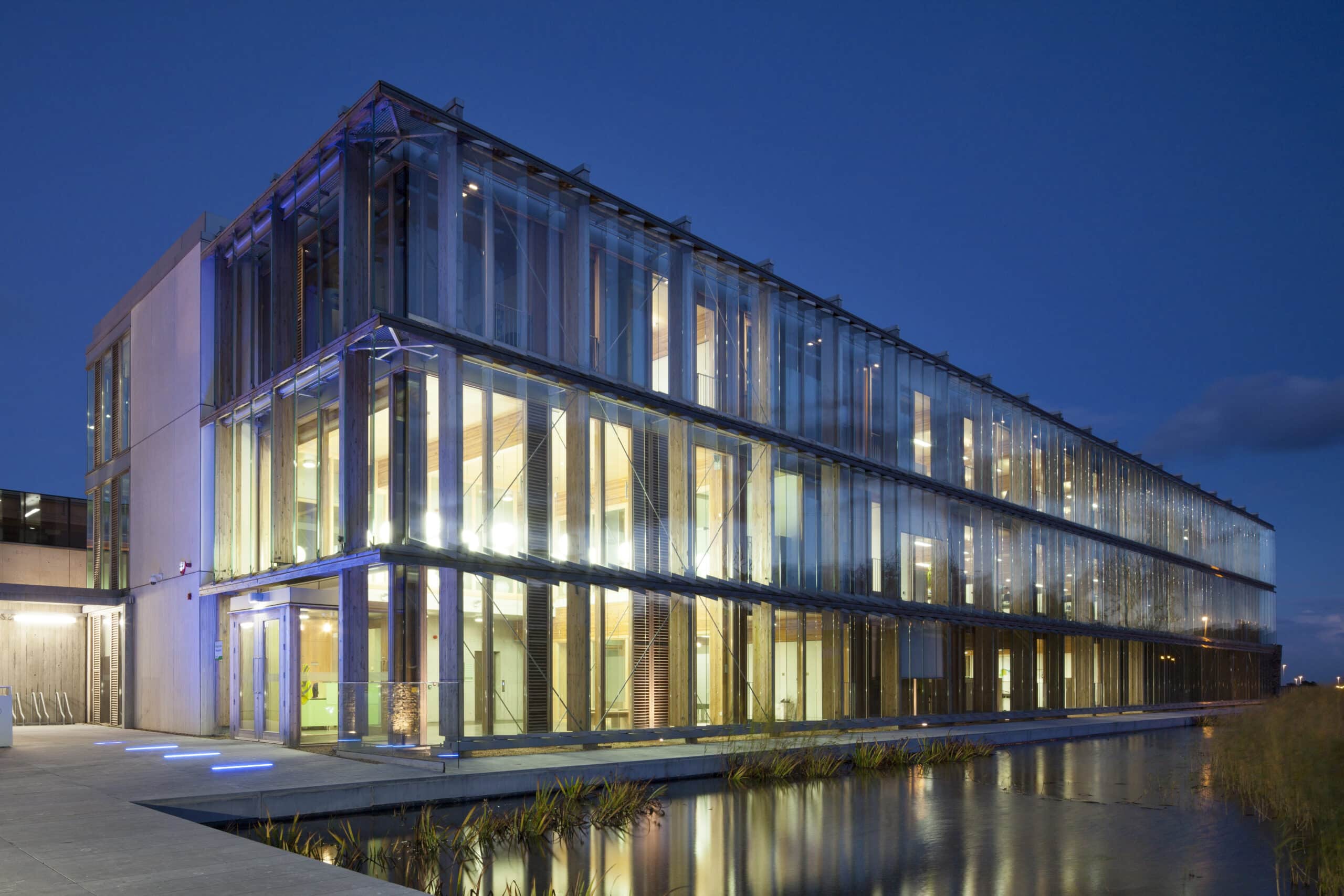
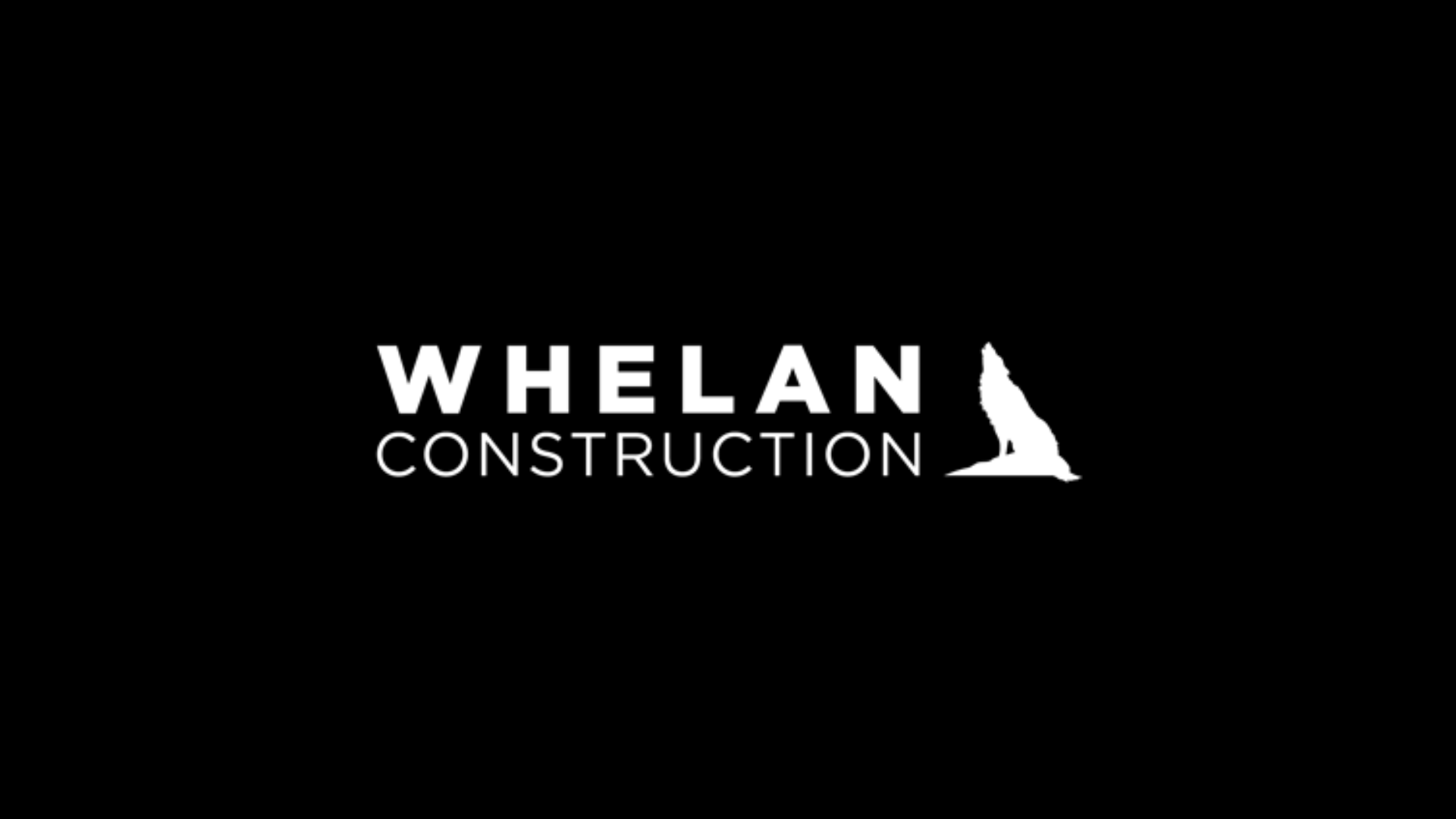
Whelan Construction is a general contracting and construction management organization that specializes in end-to-end construction services. They serve Metro Vancouver, Fraser Valley, and Squamish-Lillooet regions and specialize in Institutional, Healthcare, Light Rail, Airport, Renewable Energy and Building Performance Upgrade projects in the region of $1,000,000 to $25,000,000.
Based in Vancouver, B.C., Whelan Construction has Irish roots. Founder, Brian Whelan, emigrated to Canada in 2013 and—from one west coast to another. Brian has successfully led the construction of $400,000,000 worth of projects including airport, healthcare, residential, institutional, marine, pharmaceutical, light industrial, retail, and commercial projects.
How Autodesk Construction Cloud has helped start-up Whelan Construction win bids over competitors
The Challenge
As a start-up company, Whelan Construction faced challenges in identifying the right solutions and systems that would ensure a smooth and consistent workflow process to deliver end-to-end construction services for all stages of a project.
Outside of the solution requirements, one of the biggest challenges that Whelan Construction’s founder, Brian Whelan had experienced, was selecting a suitable project and field management software package for a small to medium sized construction company, a package that seamlessly connects the field and office.
The Solution
Given Autodesk’s extensive product portfolio, SolidCAD helped Whelan Construction to determine the right software solutions that goes together with their needs and the construction industry’s best practices requirements.
With Autodesk Construction Cloud, specifically, Autodesk Docs, Build, AutoCAD, and PDF solution Bluebeam, Whelan Construction now has a common environment for all project-related data all while helping to manage projects with minimal resources and complete project entries in one platform.
Bluebeam allowed project partners to be able to mark up and collaborate on the same documents in real-time. While, Autodesk Docs + Build, one of the industry’s leading solutions made it easy for Whelan Construction’s team to work with other project stakeholders, have connected workflows, increased transparency, and track construction progress throughout the entire lifecycle of their projects.
Moreover, Whelan Construction took one-on-one training with SolidCAD on the Docs + Cost Management component of the Autodesk Build to connect project management and field execution data to cost activities to understand root causes and scope cost impacts.
The Outcome
- Whelan Construction is now able to ensure projects stay on track; improve collaboration and reduce miscommunication, potential errors, and rework. With the ability to track all issues in one place and reduce costly rework, Whelan Construction can now keep projects on schedule all while being able to manage project data and project bids.
- Aside from that, they can now develop very detailed proposals with an ability to give the preview on designs and project development stages as required, providing them a competitive edge when winning bids.
As a result, Whelan Construction was able to apply the skills obtained from training to compile professional and successful bids.
SolidCAD continues to be a resource in helping Whelan Construction grow as a construction company in this competitive market.