Success Stories
PAPER EXCELLENCE
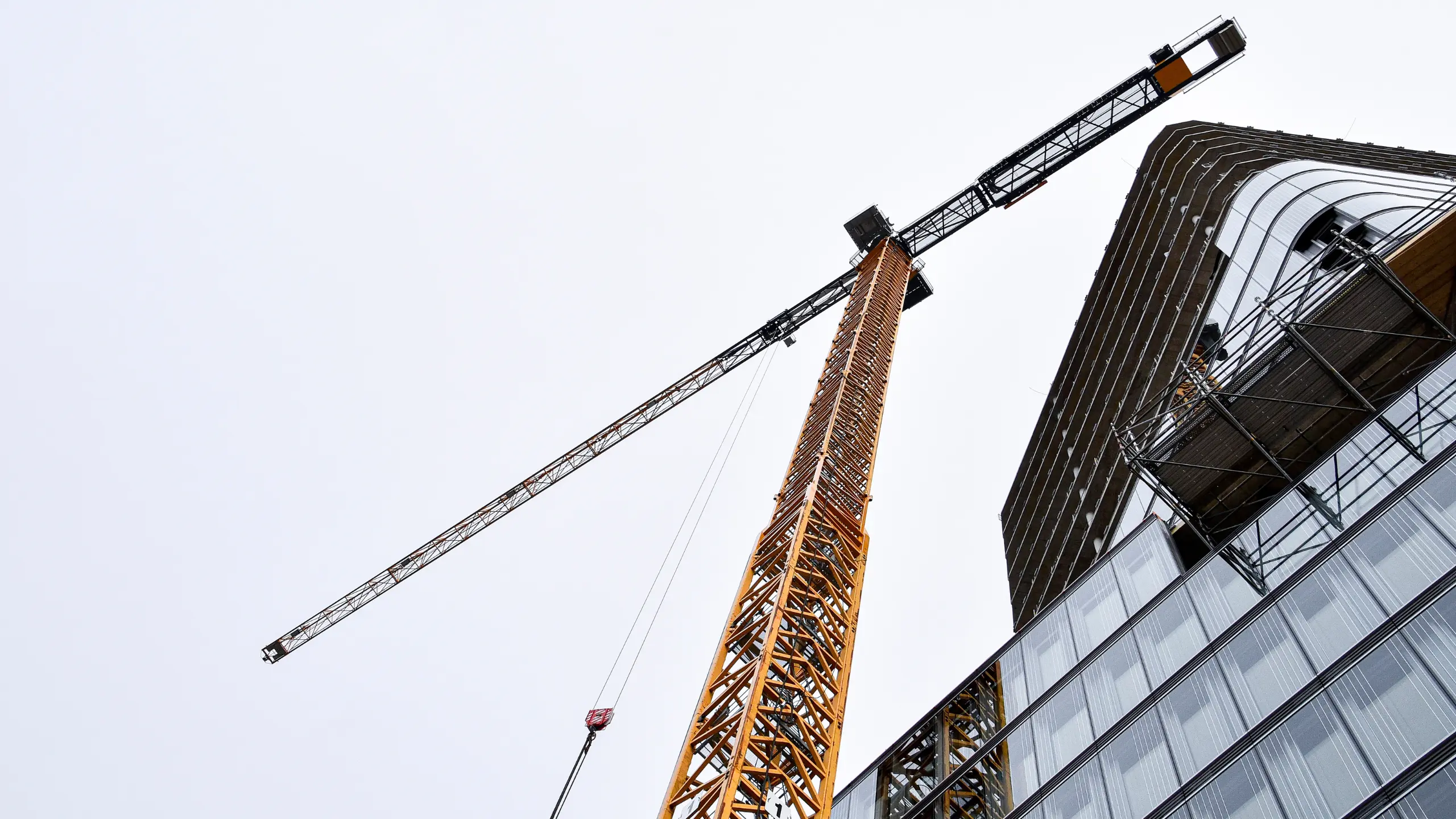
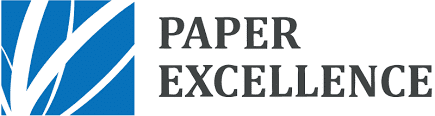
Paper Excellence is a diversified manufacturer of pulp and paper, including printing and writing, packaging, and specialty papers. We believe in the enduring value of wood-based products in global markets and have built a large network of mills and chipping plants to produce them competitively. Through our distinct approach to operational excellence, we deliver high-quality and cost-effective products to international customers.
- Over 2.5 million tonnes of production and over $2.1 billion in annual sales
- Seven manufacturing facilities in Canada
- Employs more than 2,100 people and supports another 6,200 indirect jobs
- Contributes over $4.3 billion annually to the Canadian economy
- Headquartered in Richmond, BC, Canada
Transforming Project Management with Autodesk Construction Cloud: The Paper Excellence Success Story
The Challenge
Paper Excellence faced the challenge of implementing a Project Management Platform for their recommissioning project in Prince Albert, SK. This ambitious project had the potential to generate 250 direct jobs and support an additional 1,400 indirect jobs upon its restart. To meet their needs, Paper Excellence evaluated various solutions and found that Autodesk Construction Cloud Solutions, including Autodesk Docs, Build, and Cost, offered the capabilities they were looking for.
The Solution
To address the challenge at hand, Paper Excellence worked with SolidCAD to implement a systematic and phased approach. They prioritized gaining a comprehensive understanding of the project’s goals, as well as the specific business and project requirements. This initial phase was crucial in laying the groundwork for a successful implementation.
Leveraging the insights gathered during the understanding phase, SolidCAD developed an implementation project that focused on configuring the Autodesk Construction Cloud platform to meet the specific needs identified. The aim was to tailor the platform to seamlessly integrate with Paper Excellence’s existing workflows and processes, ensuring its effectiveness and functionality.
Recognizing that successful adoption relied on proper training, SolidCAD created role-based workshops designed to provide targeted training to different team members based on their specific roles and responsibilities. By customizing the training content to address the unique needs of each role, SolidCAD aimed to enhance the team’s understanding and proficiency in effectively utilizing the Autodesk Construction Cloud.
To further enhance the learning experience and promote active participation, SolidCAD delivered the end-user training onsite. By conducting the training sessions at the project site, they created an immersive learning environment that facilitated hands-on experience and collaboration among the project team members. This approach allowed for immediate support and clarification of any questions or concerns, ensuring that Paper Excellence team could maximize their utilization of the platform.
The Outcome
The implementation of the Autodesk Construction Cloud platform led to several positive outcomes for Paper Excellence. One notable achievement was the significant increase in system usage, extending beyond the Prince Albert Project, indicating that the project team recognized the value provided by the platform.
The team’s demand for system access necessitated the purchase of additional licenses to accommodate the expanded usage. This increase in demand highlighted the effectiveness and importance of the solution within Paper Excellence’s operations. Another significant outcome was the successful centralization of all project documents within the application. By adhering to the defined workflows and leveraging the user-friendly nature of the solution, the project team ensured the organization and standardization within the Autodesk Construction Cloud. This streamlined document management process greatly improved the efficiency, collaboration, and overall performance of the Paper Excellence team.
Based on the positive experience and confidence in the Autodesk Construction Cloud along with SolidCAD’s support, the team at Paper Excellence requested ongoing assistance for a second project team as they embarked on a new venture with the build of a state-of-the-art fibre chipping facility. This request demonstrated Paper Excellence’s trust in the solution’s capabilities and their belief that the Autodesk Construction Cloud, coupled with SolidCAD’s expertise, would continue to deliver positive results for their future projects.
Testimonial
Introducing a new software platform with revised workflows is never easy. With the support of SolidCAD guiding the Paper Excellence team through the Autodesk discovery and alignment sessions, members were equipped with a clear understanding of current processes, workflows, and prepared for setup of the Autodesk Platform.
Having taken the time to work through discovery, allowed for the efficient use of time and resources when on site. Once up and running with the Autodesk Platform, our team was able to improve upon existing workflows with increased efficiencies and automation, especially within our approval processes, while at the same time, implement and deliver best practices through an organized document structure. With the setup of roles and access levels of security, our consultants and contractors move seamlessly within our platform and assigned projects, always ensuring we have the most current versions of documents and drawing sets. Further, and for auditing purposes, the tracking logs and alert features tell us what is being done, when, and by whom. SolidCAD provided our teams with support and guidance before, during and after installation, while delivering written guidance documents for all new processes developed. The experience was professional, and we look forward to adopting our next Autodesk application with confidence
– Michael Pichler, VP, Global Capital Projects & Technology at PAPER EXCELLENCE
Products & Services Used
- Autodesk Docs
- Autodesk Build
- Autodesk Cost
- Autodesk Construction Could Implementation (training, consulting, and documentation)
- Autodesk Construction Cloud Integration to SAP (working with Autodesk Partner
Morpheus)