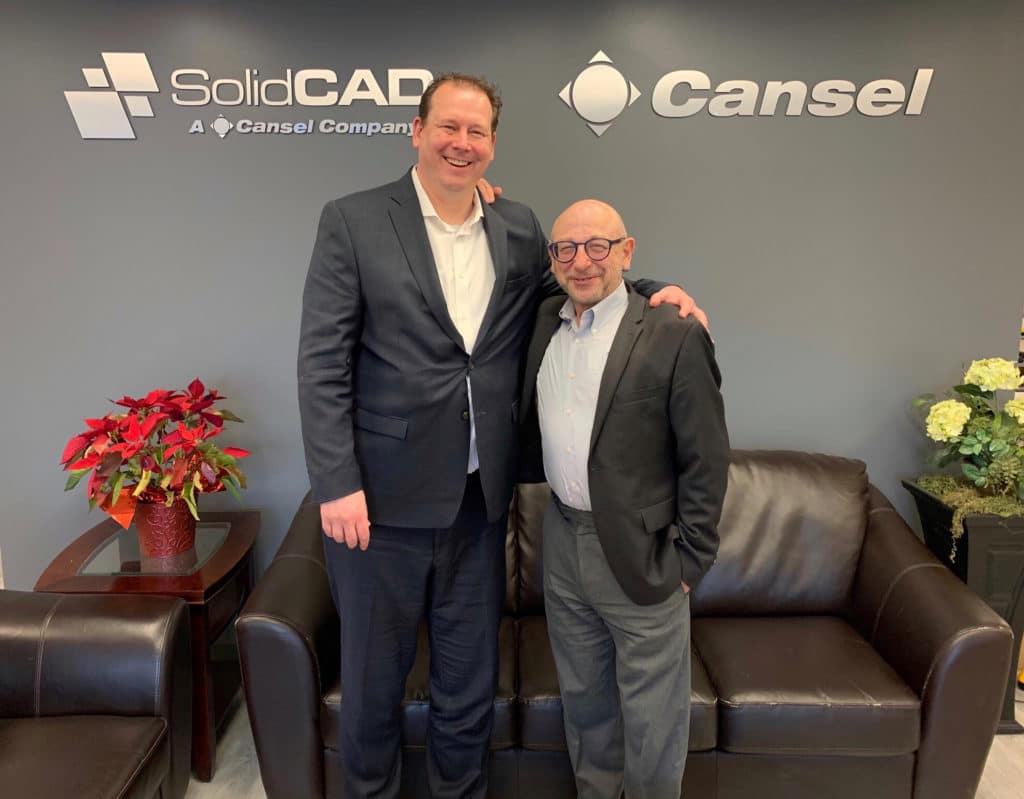
Marcus Tateishi, new President of SolidCAD being congratulated by former President, Michael Kugan at SolidCAD’s Head Office in Richmond Hill, ON.
TORONTO, ON, January 31, 2020 – Today, the Board of Directors of SolidCAD, Canada’s largest Autodesk Platinum Partner and provider of technology and professional services, announces the appointment of Marcus Tateishi as the company’s new president.
Marcus is no stranger to the Autodesk business having worked with SolidCAD as their Senior Partner Manager at Autodesk for over 14 years. In his role as Partner Manager at Autodesk, Marcus developed a strong relationship with the entire SolidCAD team and is very familiar with the organization’s internal procedures, sales processes and strategic goals. Once he assumes his responsibilities as president, Marcus will focus on generating increased revenue, profitability and productivity in client design processes.
“This is an exciting time for our company and our partners,” states Marcus Tateishi. “I am thrilled to be taking on the role of president. SolidCAD has been aiding Canadian clients in the design industry for 25 years. Over these past 14 years, I’ve witnessed the company, our employees and customers all experience incredible growth. We have become the clear leader in providing Autodesk, Bluebeam and a host of other technology solutions to the Canadian design market. I look forward to leading this dynamic team as we enter our next chapter. We will continue to provide great products and services helping our customers design, construct and manufacture a more connected and sustainable world.”
Michael Kugan, who established SolidCAD in 1996 and has been the company’s president until now, will step down and assume the position of Corporate Director starting February 1, 2020. Michael will work closely with Marcus to ensure that his transition to the presidency is seamless.
“Over the years that Marcus has been our Autodesk Senior Partner Manager, he has long been considered a member of the SolidCAD team and a valued resource,” states Michael Kugan. “With his familiarity of our brand and strong relationships with our employees, Marcus proves to be a perfect fit for SolidCAD that will help maintain our company culture, strong foundation and devotion to client success. His expertise and knowledge in the technology industry, and specifically Autodesk, will bring us a new perspective that will help our clients deliver better productivity results through collaboration. We are excited to officially welcome him onboard as part of the SolidCAD family.”
Michael Kugan, Marcus Tateishi and Alexandre Laporte, Vice President of Sales, will serve on the Board of Directors of SolidCAD. The organization will focus on continuous growth through their quality services, training and support for the technology industry.