Many “free“ content management solutions are available in the market today, such as SharePoint, Box, Network Shares, and even USB external drives. Organizations recognize the need to capture their electronic documents online and use these tools to fill the need. While providing basic functionality, “free“ applications can cost your business more money and time than a dedicated engineering document management system (EDMS).
While seeming to be a cost-effective solution, the reality is these “free” tools are missing a considerable amount of standard EDMS functionality. Here are just a few examples:
- Document control
- Workflow automation
- Full change management
This lack of features can cost money to your organization and cause lost knowledge with staffing turnover and retirement.
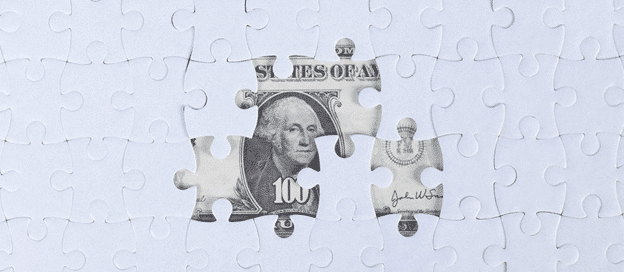
Where “Free” Document Management Tools can work and their Limitations
Some businesses can have success using document management solutions such as SharePoint, Box, and other file share applications if they fall into the following categories:
- Only require basic document management functionality
- Small or mid-sized organization
- No need to collaborate across different departments or external sources
These tools tend to work as sizeable digital filing cabinets, allowing groups to share and save documents in an accessible space and provide the following benefits for non-technical documents:
- Provide users the ability to save, share, and search for files across the business
- Cloud-based sync storage of files
- Mobile device access to documents
- Easy management of landing pages, libraries, and lists
Where “Free” Document Management Tools Fail Engineering Requirements
While these “free” tools fill a niche role, they do not provide a complete solution required by an Enterprise-class organization that requires structured, controllable document management.
A “free” tool can assist organizations that utilize a basic linear workflow for generic documents, but technical documents and drawings require a malleable workflow. Technical documents usually are highly regulated with a control process in place.
Technical documentation also comes with the following challenges:
- Normally unstructured data set
- Used across multiple systems and teams
- Difficult to access due to change management locks and file type diversity
These factors make engineering documentation tough to manage, access, and control. When you add in other systems, such as a CMMS tool, it is challenging to monitor this information within the limitations of a free tool.
Getting this wrong can have a significant impact and reverberating effects throughout multiple teams. In document-heavy facilities (i.e., power plants, factories, etc.), technical information must be accurate and available to avoid downtime and maintenance issues, leading to lost revenue. Businesses trying to shoehorn these free tools into their typically experience the following problems:
- Increased costly downtime
- No integration available between other systems such as CMMS
- Increased complexity of change process management
- Concurrent engineering challenges with technical documents
- Lack of communication tools across multiple sites and departments
- Lowered efficiency due to missing EDMS functionality
The True Value of Meridian EDMS
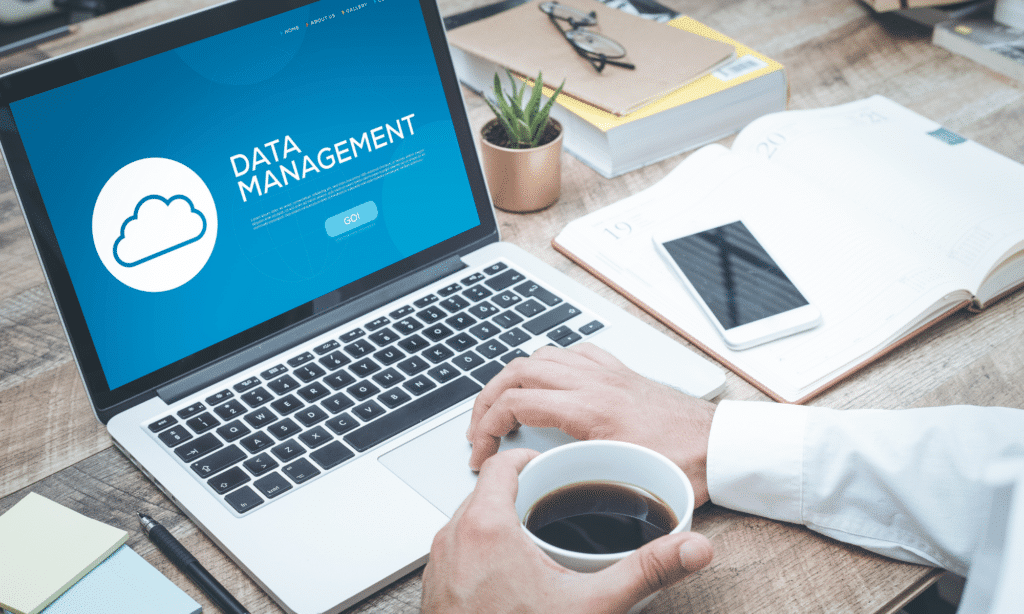
A robust engineering document management solution (EDMS) like Meridian is required to help organizations manage their technical data and avoid the pitfalls of “free” tools. While having an initial higher cost, EDMS solutions provide a considerable value when looking at the overall picture. Here are a few benefits gained by using a dedicated EDMS:
1) Document Exchange
Larger projects bring the challenge of sharing documents with multiple departments and teams. These documents can be lost or delayed when being pushed through the review cycle. An example of this is an AutoCAD file with external references. Drawings referenced by the target document can be ignored or lost during a typical workflow unless tightly tracked throughout the process.
Meridian solves this issue by tracking these secondary technical documents with built-in functionality. Free tools such as network shares or Dropbox do not cover these scenarios, leading to lost or duplicated work.
2) Extra IT Maintenance Costs
While a “free” tool can seem cost-effective, it often strains IT resources assigned to manage them. Typically, the IT resource tasked with maintaining this tool is responsible for many other systems and lacks the proper training.
The Meridian SaaS offering provides all maintenance, support, and upgrades which removes the added workload from your IT resources.
3) Work Order Efficiency
While “free” tools can help a smaller business execute on work orders, they become a hindrance to a larger organization with multiple teams and facilities. Work orders can be challenging to locate across multiple disparate systems with inadequate search tools, which can lead to the following:
- Safety concerns
- Multiple document copies spread over different systems
- Technicians using obsolete document versions
- Inaccurate data due to lack of document control tools
With a dedicated EDMS like Meridian, your organization can refer to a single source of truth that features purpose-built document control. Technicians will gain access to the latest document version that is found easily using robust search capabilities. All technical documents related to an asset can be located quickly via a tag scanner or the surrounding metadata via the advanced search. Streamlining this process will have an immediate impact on work order costs and resource availability.
4) Lower Operating Costs
Using “free” tools alongside legacy pen and paper document solutions incur costs associated with printing and logistics. When you need to get a hard copy into the hands of a critical resource on time, this can impact your budget. Not only can this cost your business money, but it also wastes effort if the package does not contain all the required documents.
The Meridian solution will allow your teams to move critical data into a single system with high online availability. Moving to an EDMS will allow your resources to access the latest complete document packages on many IoT platforms (i.e., mobile devices, tablets, PCs). Manual labor is heavily reduced via the automation capability of the tool, saving many hours in labor costs.
Sometimes “Free” is Expensive
The actual cost of a “free” or legacy tool can surprise an organization. By not using a purpose-built application to manage your technical documents, you can end up costing your business time, efficiency, and money in the big picture.
If your business is interested in unlocking the power of a dedicated EDMS, don’t hesitate to get in touch with the SolidCAD Meridian team.